Understanding Plastic Injection Molding: A Gateway to Efficient Manufacturing
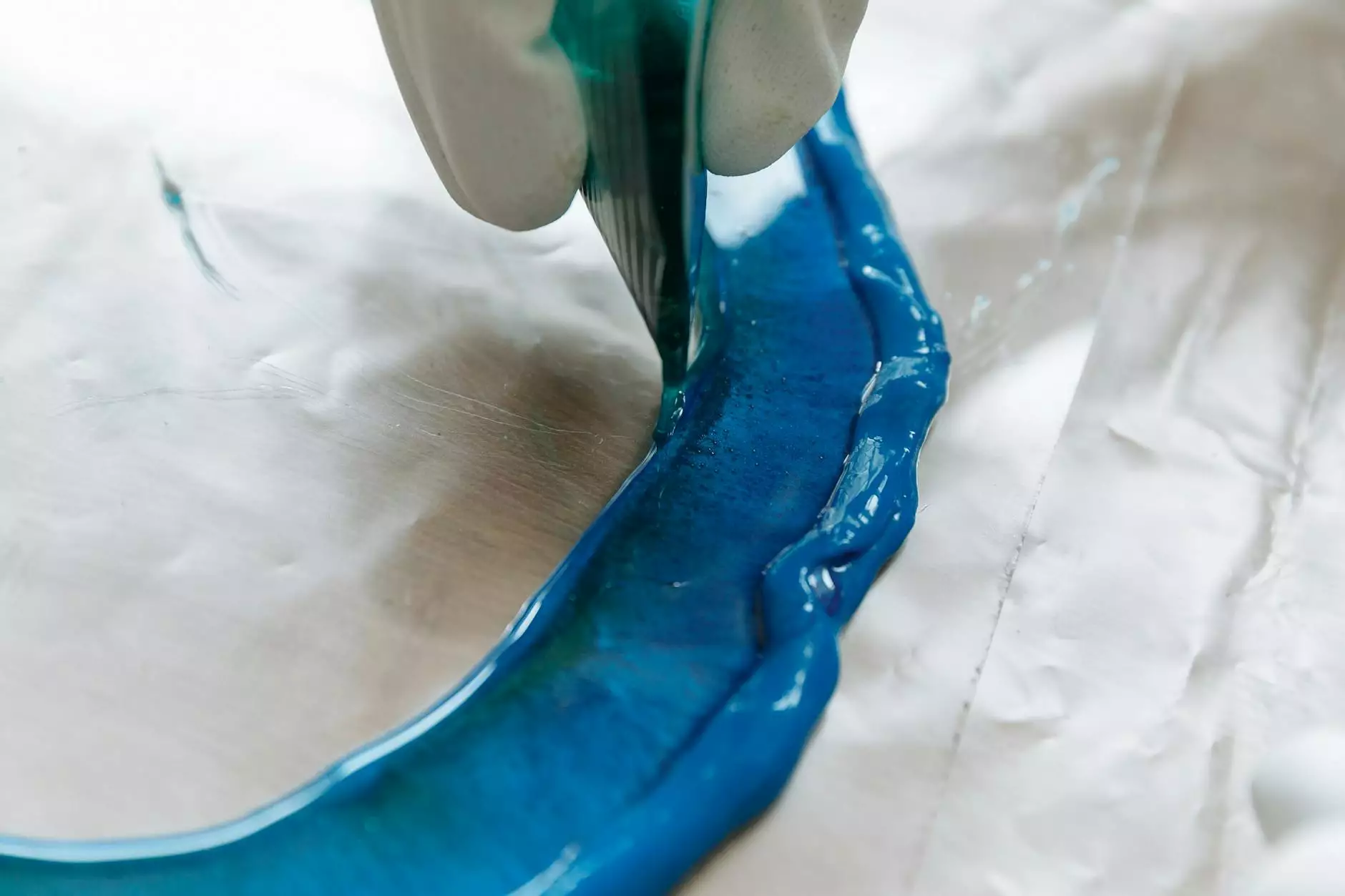
Plastic injection molding is one of the most popular manufacturing processes utilized today. It is a technique that allows manufacturers to create complex shapes and components from plastic with remarkable precision and efficiency. At Sumiparts, we specialize in providing high-quality industrial supplies, including services in machining, laser cutting, welding, and of course, plastic injection molding.
The Basics of Plastic Injection Molding
Plastic injection molding involves melting plastic material and injecting it into a mold where it cools and solidifies into the desired shape. This method is particularly favored for its ability to produce large volumes of parts with high dimensional accuracy.
Key Steps in the Plastic Injection Molding Process
- Material Preparation: The process begins with selecting the right type of plastic, often in the form of small pellets. These pellets are then dried to remove moisture, ensuring optimal melting and flow.
- Melting the Plastic: The pellets are heated to a specific temperature until they reach a molten state. This allows the plastic to flow easily into the mold.
- Injection: The molten plastic is injected into a mold cavity under high pressure, filling the designated spaces. The speed and pressure used can significantly impact the finish and characteristics of the final product.
- Cooling: Once the mold is filled, it is allowed to cool. The cooling time depends on the material and thickness of the part being produced.
- Mold Opening: After cooling, the mold is opened, and the formed plastic part is ejected from the mold cavity.
- Trimming and Finishing: Finally, any excess material or imperfections are trimmed, and additional finishing processes may be applied to enhance the product’s features.
Advantages of Plastic Injection Molding
The popularity of plastic injection molding stems from its various advantages, which make it an ideal choice for numerous industries:
- High Efficiency: The process allows for rapid production cycles, which translates into lower manufacturing costs for high-volume parts.
- Design Flexibility: Complex shapes with intricate details can be created easily, making this method suitable for a wide array of applications.
- Consistent Quality: Once set up properly, the process produces parts with exceptional uniformity and precision, reducing the need for extensive quality control.
- Material Variety: A broad spectrum of plastic materials can be used, such as thermoplastics and thermosetting polymers, which can be selected based on the application’s requirements.
- Minimized Waste: Since the molding process is highly efficient, it produces minimal waste compared to other methods like machining or cutting.
- Automation Potential: Plastic injection molding can be easily automated, leading to increased efficiency and reduced labor costs.
Applications of Plastic Injection Molding
The versatility of plastic injection molding allows it to be utilized across various industries. Here are some notable applications:
1. Consumer Products
From toys to kitchenware, consumer products benefit greatly from the design flexibility and cost-effectiveness of injection molding.
2. Automotive Industry
In the automotive sector, injection-molded parts such as dashboard components, trim pieces, and even functional parts are produced due to their durability and aesthetic appeal.
3. Healthcare and Medical Devices
Medical devices, including disposable syringes, medication containers, and complex machinery components, often utilize injection molding to meet strict hygiene and accuracy standards.
4. Electronics
Plastic injection molding is essential in creating housings, connectors, and other electronic components, ensuring quality and reliability in electronic products.
5. Industrial Equipment
Components for machinery, equipment housing, and connectors in industrial settings can be efficiently produced through this process, enhancing the overall functionality and reliability of the equipment.
Choosing the Right Manufacturer for Plastic Injection Molding
To ensure the best results, selecting the right manufacturer for your plastic injection molding needs is crucial. Here are some factors to consider:
- Experience: A manufacturer with extensive experience in plastic injection molding is more likely to deliver quality results.
- Capabilities: Ensure the manufacturer possesses advanced machinery and technology to handle your specific requirements.
- Material Expertise: Knowledge of different plastic materials can significantly influence the quality and suitability of the products being manufactured.
- Quality Control: A robust quality control system should be in place to minimize defects and ensure consistent quality in production.
- Customer Support: A responsive and knowledgeable customer support team can help address any queries or concerns throughout the manufacturing process.
Sumiparts: Your Trusted Partner in Plastic Injection Molding
At Sumiparts, we pride ourselves on our exceptional service and commitment to quality in all our industrial supplies, including plastic injection molding. Here’s why we stand out:
- Comprehensive Solutions: We offer a complete range of manufacturing services, from machining and welding to laser cutting and vulcanization, ensuring all your industrial needs are met.
- State-of-the-Art Technology: Our advanced machinery and skilled workforce enable us to produce high-quality plastic components tailored to your requirements.
- Custom Solutions: We specialize in providing customized injection molding solutions that cater to various industries, with a focus on excellence and innovation.
- Commitment to Quality: Our rigorous quality control measures ensure that you receive only the best products, meeting all industry standards.
- Expert Guidance: Our team of experts is always ready to assist you in selecting the right materials and processes for your specific applications.
Future Trends in Plastic Injection Molding
The future of plastic injection molding looks promising with advancements in technology and increasing demand for sustainable practices. Here are some trends to watch:
1. Sustainable Practices
With growing environmental concerns, many manufacturers are shifting towards sustainable materials and processes, reducing waste and utilizing recyclable and bio-based plastics.
2. Smart Manufacturing
The integration of IoT and automation in manufacturing processes is creating smarter, more efficient production lines, enhancing overall productivity.
3. Advanced Materials
Developments in materials science are leading to the creation of new, high-performance plastics that can withstand more extreme conditions, expanding the application range of injection-molded products.
4. Customization and On-Demand Production
Advancements in rapid prototyping and 3D printing are leading manufacturers to offer more customized and on-demand production solutions, catering to specific customer needs.
Conclusion
Plastic injection molding is a vital process in modern manufacturing, offering numerous advantages in efficiency, precision, and versatility. Whether you're operating in the consumer, automotive, healthcare, or industrial sectors, choosing the right manufacturing partner is essential to harnessing the full benefits of this process.
At Sumiparts, we are committed to providing top-tier services in plastic injection molding and other industrial solutions. Our expertise, state-of-the-art technology, and commitment to quality ensure that your manufacturing needs are met with excellence.
Explore the full range of our services today, and discover how we can elevate your production capabilities through our comprehensive industrial supplies.