The Importance of China Prototype Injection Molding in Modern Manufacturing
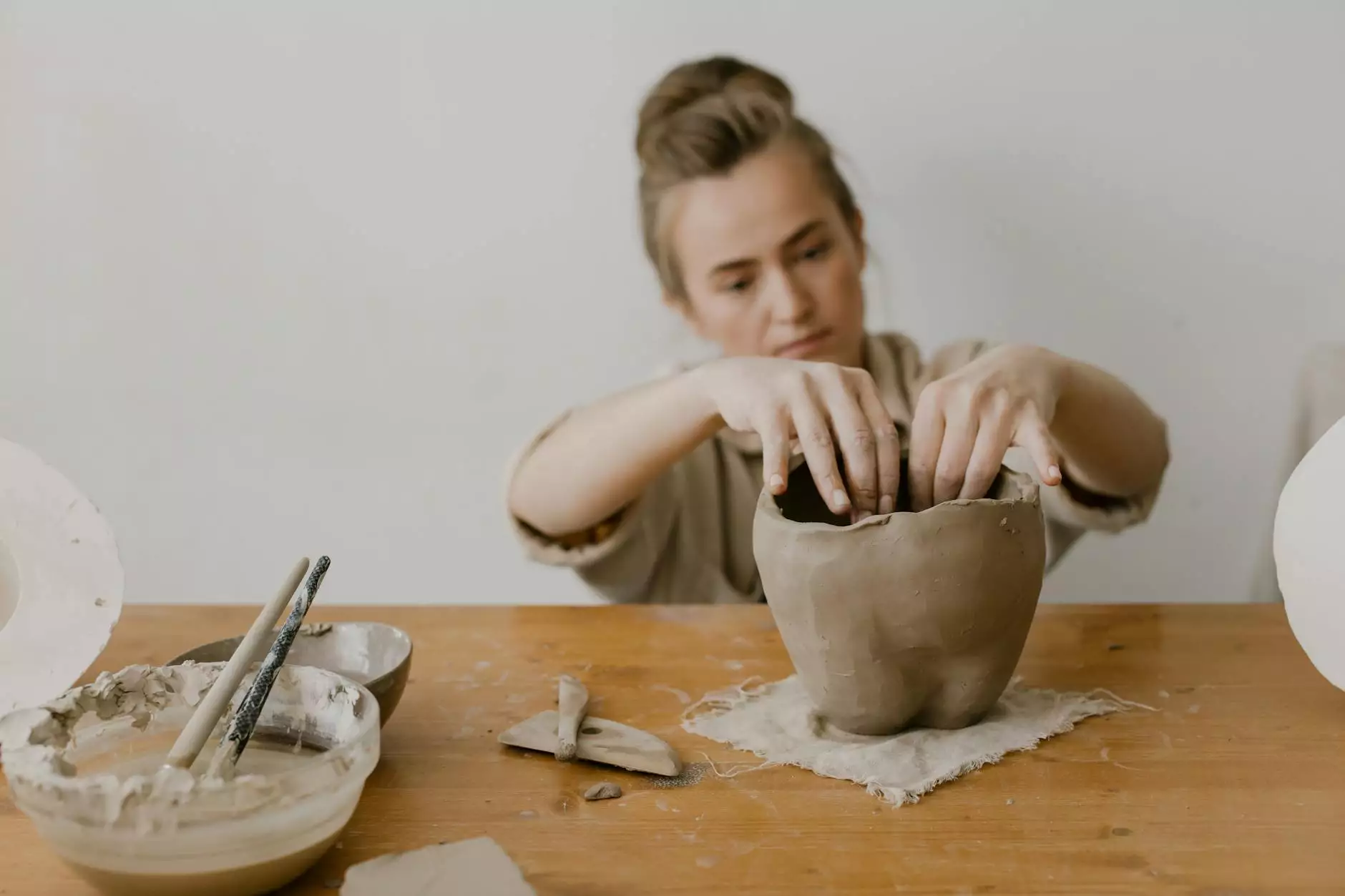
The dynamic world of manufacturing is continually evolving, with new technologies and processes emerging that aim to enhance productivity and quality. Among these, China prototype injection molding stands out as a paramount technique that enables businesses to develop prototypes efficiently. This article dives deep into the intricacies of injection molding in China, highlighting its significance in the manufacturing sector, and elaborates on why choosing this method can be a game-changer for your business.
What is Prototype Injection Molding?
Prototype injection molding is a specialized manufacturing process that involves creating a mold from a digital design, into which plastic is injected to produce a prototype part. This process enables engineers and designers to create high-fidelity models of their designs quickly, allowing for functional testing and validation before moving on to mass production.
How Does Prototype Injection Molding Work?
The process of injection molding, especially in the realm of prototypes, typically involves several key stages:
- Designing the Mold: The first step is to create a detailed design using CAD (Computer-Aided Design) software. This design includes all specifications and dimensions intended for the final product.
- Creating the Mold: After the digital model is finalized, the mold is crafted from durable materials, typically steel or aluminum, which can withstand high pressures and temperatures.
- Injection Process: Once the mold is ready, molten plastic is injected into the mold cavity at high pressure. This ensures the plastic fills all intricate details of the mold.
- Cooling and Ejection: The injected plastic is allowed to cool and solidify before the mold opens and ejects the prototype. This process usually requires only a few minutes, allowing for rapid production cycles.
- Post-Processing: After ejection, the prototypes may undergo finishing processes such as sanding or painting to achieve the desired aesthetics and functionality.
Advantages of China Prototype Injection Molding
Leveraging China prototype injection molding offers a plethora of advantages, particularly for businesses looking to innovate and reduce time-to-market. Some of these benefits include:
1. Speed and Efficiency
One of the most significant benefits of injection molding is the remarkable speed at which prototypes can be produced. Annually, thousands of prototypes can be generated within rapid turnaround times, enabling companies to expedite the product development cycle efficiently.
2. Cost-Effectiveness
China has lower manufacturing costs due to affordable labor and material price advantages, making it an attractive destination for these services. This cost efficiency translates into significant savings on the overall prototyping budget.
3. High Precision and Reproducibility
Injection molding allows manufacturers to achieve a high degree of accuracy and detail in the prototype, which is pivotal for testing and validation. The initial prototypes can closely resemble the final products, ensuring that any adjustments can be precisely implemented.
4. Material Versatility
The process supports a wide variety of materials from plastics to advanced composites, enabling designers to choose the best material for their intended application. This versatility is particularly beneficial in industries that require specific material properties, such as heat resistance or flexibility.
5. Design Flexibility
Design iterations can be carried out swiftly, allowing for modifications based on testing feedback without lengthy delays. This adaptability fosters innovation and creativity during the prototyping phase.
Challenges in Prototype Injection Molding
While China prototype injection molding is a revolutionary method for rapid prototyping, several challenges may arise, including:
- Initial Costs: The initial setup cost for creating molds can be high, particularly for complex designs. However, this investment is often justified by the savings realized during mass production.
- Lead Time for Molds: Although prototypes can be produced quickly, crafting the initial mold can take time, which may delay the overall project timeline.
- Material Selection: Choosing the correct material is essential to ensure the prototype’s performance matches the end goals. Poor choices can lead to the need for additional iterations.
Why Choose Deep Mould for Your Prototype Injection Molding Needs?
When considering a manufacturing partner for your China prototype injection molding requirements, Deep Mould stands out for numerous reasons:
1. Expertise and Experience
Deep Mould has extensive experience in the field of injection molding, equipped with a team of skilled professionals who have years of expertise in handling diverse projects across various industries.
2. Advanced Technology
The company utilizes state-of-the-art machinery and technologies, ensuring that you receive the highest quality prototypes. This technological edge facilitates the production of intricate designs that meet stringent specifications.
3. Comprehensive Services
From design consultation to post-processing, Deep Mould provides a comprehensive suite of services. This means you can streamline your supply chain by dealing with a single provider for all prototyping needs.
4. Fast Turnaround Times
Understanding the importance of speed in product development, Deep Mould emphasizes quick delivery without compromising quality, ensuring you get your prototypes when you need them.
5. Client-Centric Approach
Deep Mould is dedicated to client satisfaction, working closely with you to understand your needs and tailor solutions that fit perfectly with your project goals.
Conclusion
In summary, China prototype injection molding serves as a pivotal process in modern manufacturing. By choosing this method, businesses can enhance their product development capabilities, achieve significant cost savings, and ultimately bring their innovative products to market faster. With trusted partners like Deep Mould, you can ensure that your prototype development journey is smooth, efficient, and aligned with your business objectives. Take the leap today and embrace the potential of injection molding to propel your business forward!